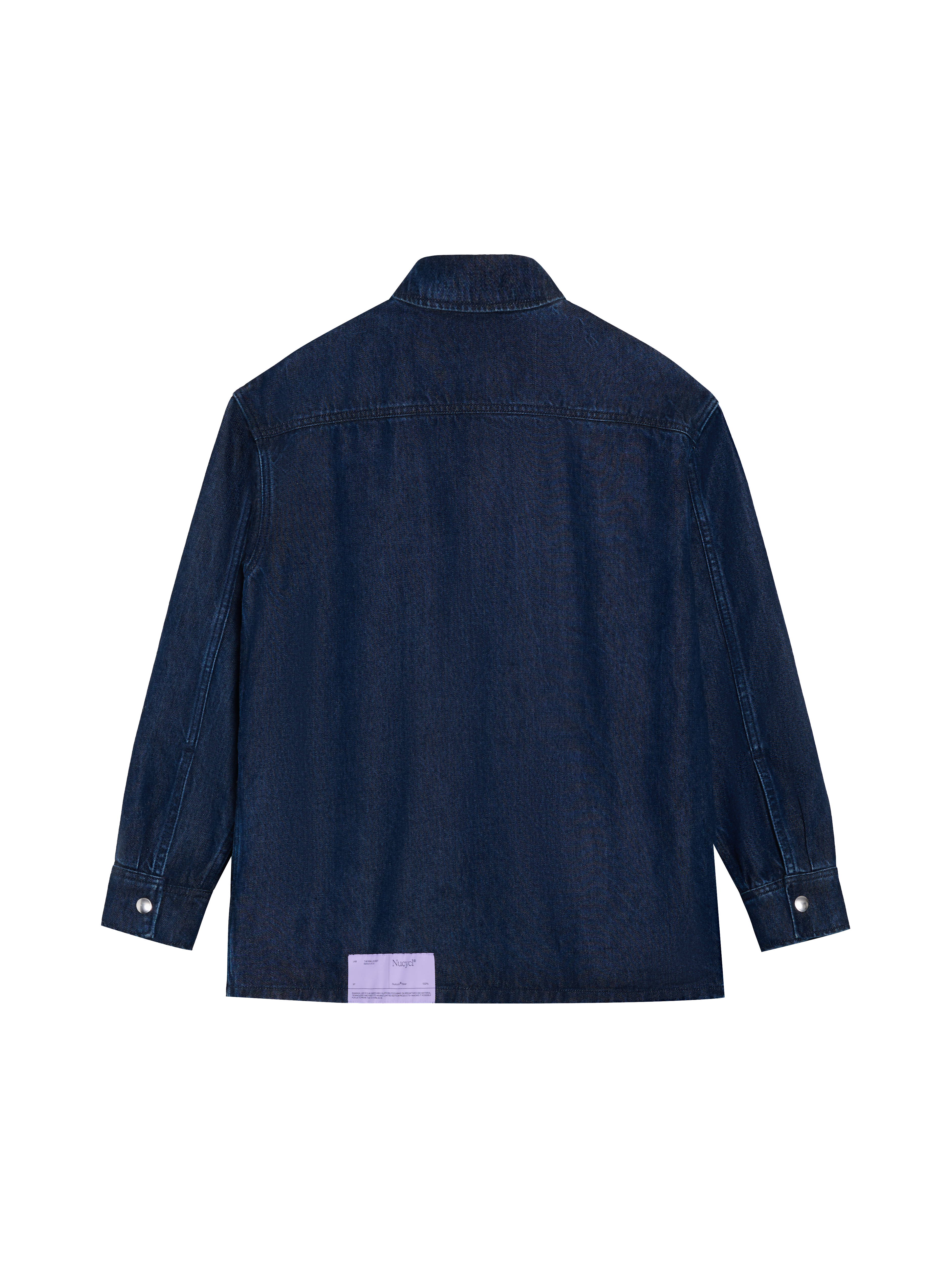
- |
- PRESS COVERAGE
Denim Drops From Pangaia, Diesel and Progress Updates for 'Fashion Act': Short Takes
Denim Drops: The denim days aren't over just yet if new collaborations are any indicator.
Our Nucycl® technology converts cotton waste into new fiber, which can be reformed again and again.
Discover MoreBy Abigail Turner
Materials science brand Pangaia has launched its first denim product made entirely from cotton textile waste. Abigail Turner speaks to Pangaia Lab about its collaboration with textile innovations company Evrnu.
Materials science brand Pangaia has launched its RENU jacket in collaboration with textile innovations company Evrnu.
The New York-based brand created the product with Evrnu’s NyCycl material, making it the first denim product in the Pangaia range made entirely from cotton textile waste.
The Pangaia Lab team says: “We wanted to test if we could displace something as ubiquitous as cotton denim with a 100% recycled and 100% recyclable solution.”
Evrnu, which recently launched its first direct-to-consumer (DTC) product, created NuCycl from pre- and post-consumer textile waste. The US-based company says it is up to four times stronger than other cellulosic fibres, including cotton and most MMCF, and can be recycled up to five times without loss in performance or quality. Using NuCycl helps divert textile waste away from landfill and incineration and reduces the industry’s reliance on cotton, MMCF, nylon, and polyester.
Pangaia says it intends to continue working in partnership with Evrnu, using NuCycl in more fabrications and products throughout the range. Pangaia’s Pangaia Lab is the brand’s discovery platform bringing advanced technology to lifestyle goods. The partnership with Evrnu came out of a shared desire to find replacements for high-resource fibres such as cotton, and to harness the value of materials already in circulation, rather than fossil fuel, animal-derived, or virgin fibres.
The RENU jacket is the first denim product to be made with NuCycl. Pangaia Lab says: “At times, we develop our own proprietary technologies to provide solutions to the industry that we don’t see solved elsewhere.”
Using the example of the Flwrdwn, the lab adds: “This is a patented, high-performing and animal-free replacement for traditional animal and petroleum-based synthetic down and fillings. Otherwise, we are proud to work in collaboration with the most promising up-and-coming innovators, such as Evrnu, acting as a scaling partner in their path to commercialisation.”
The main challenge for the brand came when transitioning from small-scale prototyping to large-scale production “while maintaining consistency and quality”.
Pangaia Lab says: “We optimised manufacturing processes, sourced reliable suppliers, and ensured scalability without sacrificing innovation or cost-effectiveness – these were key considerations that we worked collaboratively with our partners on to mitigate challenges faced at the point of commercialisation.”
Pangaia Lab has commercialised a series of first innovations in material science including launches with Colorifix, Twelve, Spiber, Infinited Fiber, Evrnu, C16 Biosciences, Natural Fiber Welding, and Zellerfeld.
The brand was recently awarded a Fair Wear Leader score, gaining industry recognition as a leader in building an ethical supply chain, and achieved a BCorp score of 84.5 in 2022, after only three years of operating as a business.
Pangaia Lab says: “We are committed to shifting our business models to reduce environmental harm by decoupling growth from resource consumption and pollution. Underpinning our work is eliminating waste and pollution in our supply chain and operations; circulate products and materials; and regeneration of nature.”
The World Economic Forum estimates between 80bn and 150bn units of clothing are manufactured every year. This figure is likely to only increase as ultra-fast fashion brands such as Shein flood the market with thousands of new styles a day.
Only 1% of recycled clothes are turned back into new garments, according to McKinsey. This, the management consultancy says, is a “missed revenue opportunity of more than US$100bn a year”, not including the additional high costs for landfilling and incineration.
Coupled with global regulations calling for more environmental protocols in the textile industry, such as Members of European Parliament (MEPs) recently voting to strengthen a proposed extended producer responsibility (EPR) scheme for textile waste, manufacturers and retailers are looking for better of end-of-life solutions for textiles.
In September 2023, Pangaia launched a first-of-its-kind, digital passport-enabled community-driven peer-to-peer resale platform ReWear.
Pangaia Lab says: “Pangaia seeks to empower its community to engage with circularity at every stage of the garment’s life, fostering a more sustainable and responsible relationship with clothing. It is our ambition to ensure that we are manufacturing products using nontoxic and closed-loop processes, while also using technologies to design waste out further upstream.
“Our partnership with Evrnu and the creation of the Renu Jacket is a perfect example of our product launch that drew industry and customer attention to the problems associated with waste in our industry, and offered a commercial solution when the positive impact is built into the product design.”
Evrnu’s cycle starts with used cotton-rich textiles and production waste. The company then works with textile recyclers, brands and retailers to source this waste. It is then shredded, liquified, purified and transformed into NyCycl lyocell fibre. The new regenerative fibre can be recycled again and again to make new products over and over.
Evrnu is planning its first commercial manufacturing facility, which is due to be completed this year. It is hoped that once built it will have the ability to create 18,000 tonnes of NuCycl fibre per year, reducing cotton waste and avoiding landfill gas emissions, with a carbon footprint of -25,000 carbon dioxide equivalent (CO2e). The same amount of cotton production would typically consume over 36 million tons of water, whereas NuCycl will consume less than half a million.
Evrnu fibres are soft, absorbent and “stronger that virgin cotton and polyester”. They can be used across a range of apparel sectors including footwear and outerwear. Pangaia Lab says its mill partner Orta Andalolu dyed the NuCycl denim with natural indigo, finding that it took the dye well and was able to be washed down to achieve “the natural highs and lows found in traditional workwear”.
Elsewhere, Pangaia Lab has expanded to use of its “more circular innovative dyeing and finishing technologies”, through its Pangaia Re-Color Capsule. In this range, the products are made with Recycrom, an innovative technology dye that pulverises textile scraps into coloured powder dyes. The coloured powder dyestuffs are made using 98% textile waste from Pangaia’s production leftovers helping us repurpose textile waste for a more circular system.
By clicking the button you're confirming that you agree with our terms and conditions.